Avoiding Costly Mistakes: Common Pitfalls in Mechanical Design
Introduction
Designing mechanical components or systems can be complex, and even small missteps can lead to significant issues down the line. From production delays to budget overruns, poor design decisions can cost businesses time and money. This article explores some of the most common mechanical design pitfalls and offers practical advice on how to avoid them.
1. Lack of Design for Manufacturability (DFM)
One of the biggest oversights in mechanical design is failing to consider how a part will be manufactured. Designers sometimes create idealized parts without taking into account the limitations of manufacturing processes, materials, tooling or practicality.
How to avoid it:
- Involve manufacturing experts early in the design process.
- Choose materials and geometries that are readily available and cost-effective.
- Understand the capabilities and tolerances of the machines that will produce your part.
2. Overcomplicating the Design
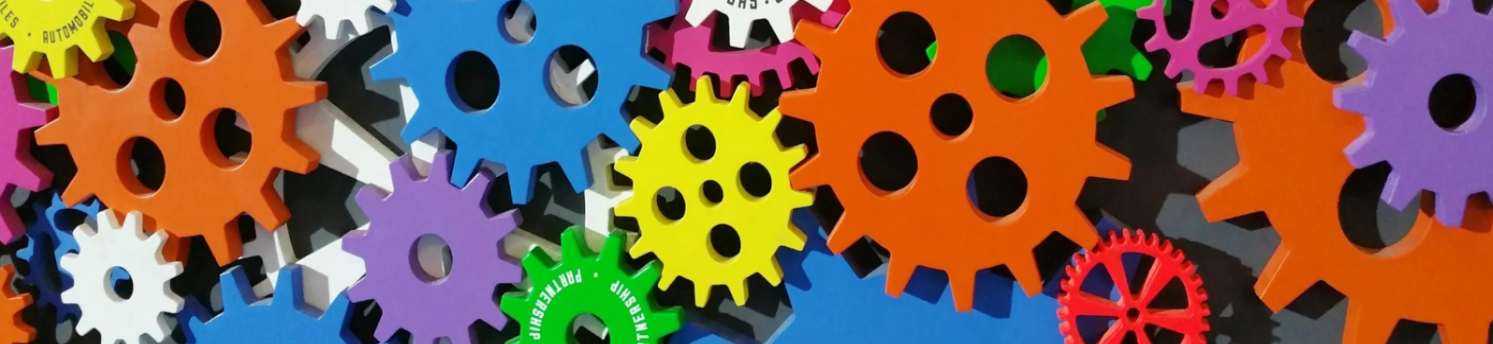
Complex designs can be aesthetically appealing or highly functional, but they often lead to unnecessary complications in production and assembly.
How to avoid it:
- Simplify where possible. A simpler design often means fewer components, faster assembly, and lower costs.
- Use standard parts where appropriate. We will allways ask or check if we can purchase a part before we seek to reinvent the wheel.
- Validate the design against real-world constraints and usability.
- Involve end users and stakeholders early, this avoids producing a design that doesn’t meet user needs
3. Inadequate Testing and Simulation
Skipping the simulation or prototyping phase to save time or money can backfire. Design flaws often reveal themselves only when a part is tested under realistic conditions.
How to avoid it:
- Use flow and stress simulations during the design phase to predict performance.
- Build and test physical prototypes if possible.
4. Poor Tolerance Stack-Up Analysis
Neglecting to analyze how part tolerances stack up can result in assemblies that don’t fit or function as intended, leading to rework or scrapped parts.
How to avoid it:
- Perform detailed tolerance analysis during the design phase.
- Collaborate with machinists and assemblers to understand realistic tolerances.
- Use CAD tools to simulate assembly fit before committing to production.
5. Ignoring Regulatory or Compliance Requirements
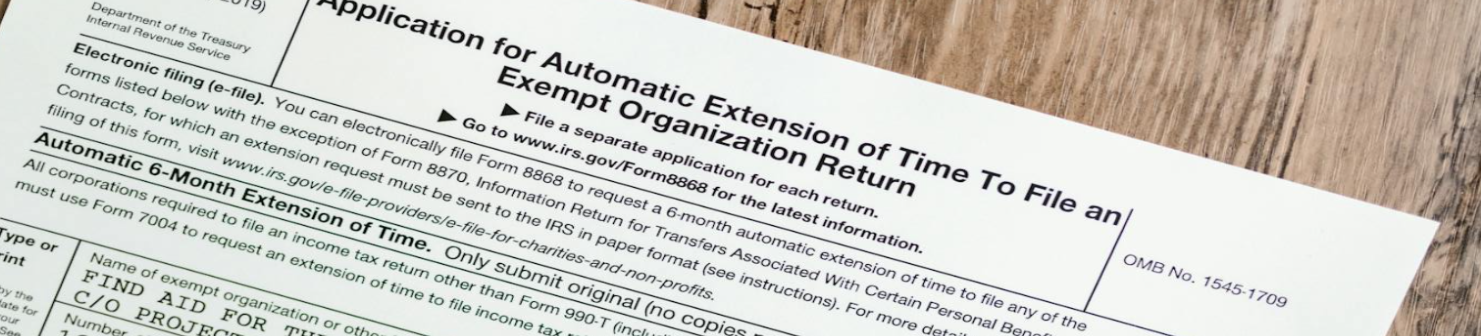
Overlooking standards and regulations can delay product approvals and market entry.
How to avoid it:
- Identify relevant compliance standards early (e.g. NZS, ISO).
- Document all decisions and specifications clearly.
- Work with a consultancy like Nexus to navigate compliance efficiently.
Conclusion
Mechanical design is as much about foresight and process as it is about creativity. By avoiding common pitfalls—such as overcomplication, lack of testing, and ignoring manufacturing constraints—you can streamline your path from concept to production. At Nexus, we help clients avoid these costly mistakes by providing expert guidance, simulation, and detailed engineering support.
Want to ensure your next design gets it right the first time? Get in touch with Nexus today.
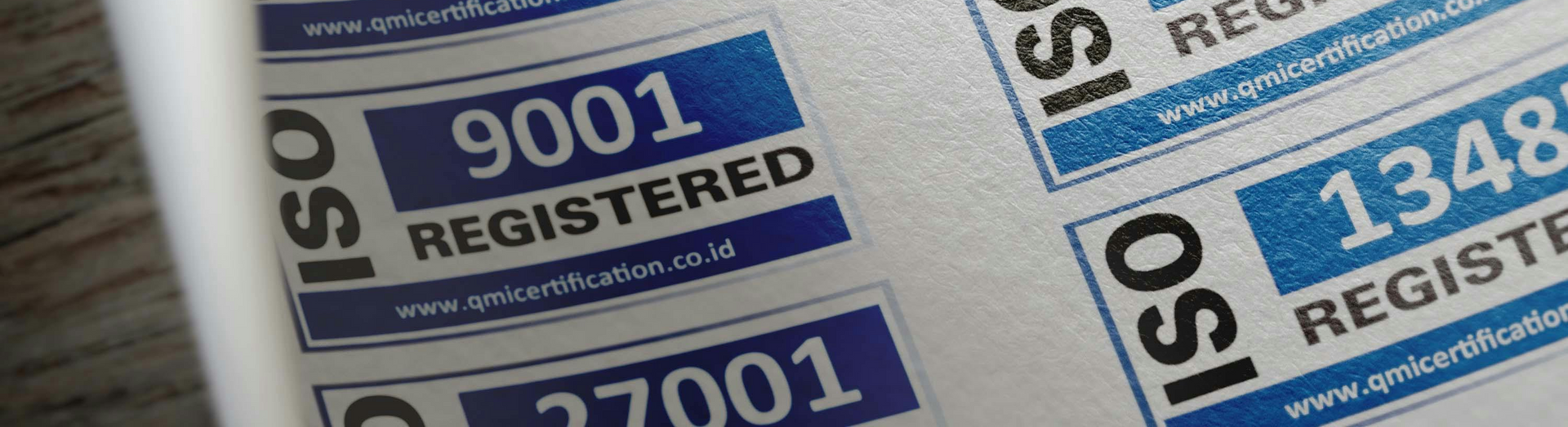